As the population keeps increasing, more and more people with disposable income require garments at bargain prices. Manufacturers are increasingly looking for garment machinery that can support them with a high production rate.
The global apparel market itself is estimated to reach around $842.73 billion in 2025 at a CAGR of 7%. Besides, its manufacturing industry reached $861.5 billion in 2022, showing a growth rate of 1.7% per year on average between 2017 and 2022.
These numbers are not surprising considering the evolving fashion trends and increasing demand for clothing. Hence, the supply is kept flowing thanks to the necessary machinery that is used in the manufacturing process and delivers high-quality garments to consumers.
What factors to consider before selecting garment equipment?
Production output capability
Undoubtedly, a piece of machinery is at its best when it produces maximum output with minimum utility requirements. This is one of the key factors in decision-making. Ensure the machinery comes at a reasonable price and its production output is worth the budget.
Product type
The product type and its primary usage play a part in large portions of decision-making. Having understood the factory requirements and knowing which equipment to purchase, it is also essential to buy high-quality and durable garment equipment that is effective and more eco-friendly.
Manpower usage
Since factories involve paying manpower by the hour for operating the machine, identifying the cost per production unit is crucial. It is best to go with garment machinery that makes workers more efficient, hence saving more time and money for the business. A factory worker will find it easy to operate a sewing machine that requires less maintenance and has a good production output compared to machinery that requires high usage and has less production output.
Power consumption
Checking the power consumption rate of the equipment is crucial—especially for long operational hours. Taking into account the cost of energy per production unit, factory owners should opt for machinery that requires a domestic phase to operate in. Or else, they will need to arrange electricity from their local Electricity Board.
Space estimation
Before installing the garment machinery or equipment, it is also important to know how much space it would take in the factory. Larger equipment like a fabric spreading machine would require more space than a sewing machine. Estimating the space first and then reserving the space for particular machinery is vital before purchasing.
Installation and training
For larger garment machinery, there may be some installation charges that come along with it. Keeping an eye on that service charge would be helpful. Some suppliers provide training to factory workers on how to use this equipment efficiently. Factory owners can benefit from this when they choose the right suppliers.
Guarantees and warranties
Before purchasing the equipment, it is important to go through any guarantees and the warranty period. Undoubtedly, machinery will experience wear and tear or other minor issues down the road, so it is ideal to know how much warranty period each supplier would give to save some maintenance costs.
Types of machines required for a garment factory
Printing machine
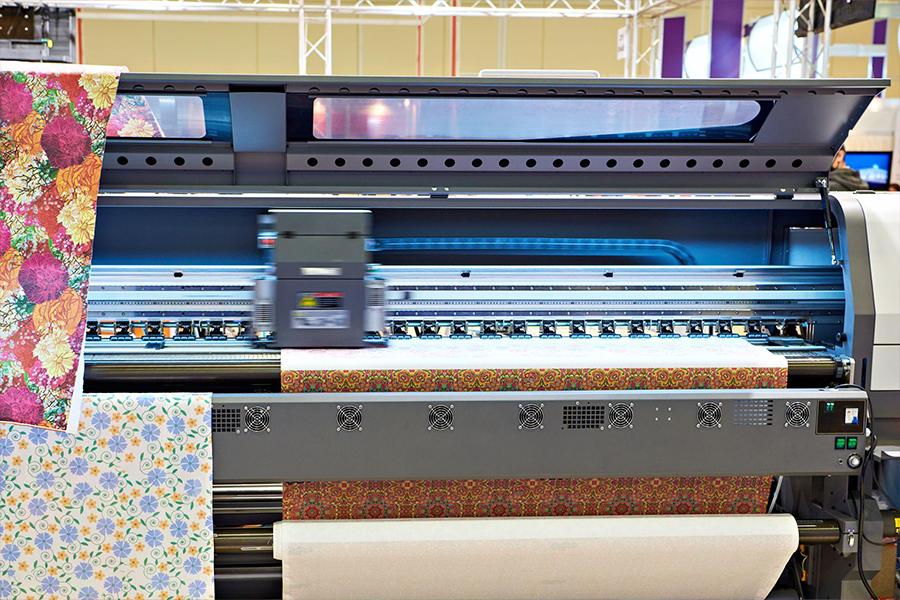
Printing machines, mainly DTG (direct-to-garment), utilize the same concept as inkjet printers. With many designs and on-print demand for fabrics, computerized printing machines transfer ink to natural fibers. DTG printing machines are quick as it takes them only a few minutes, and some can print multiple garments in quick succession. When operating a printing machine, the needle diameter, line distance, air pressure, printing speed, and pattern are a few parameters that need to be adjusted from fabric to fabric.
Fabric spreading machine

For smaller garments, it is easier to spread them by hand. However, for a large-scale garment factory, fabric-spreading machines are a necessity. A few parameters to consider when using a fabric spreading machine are the fabric facing, fabric tension, edge control, layer height, and splicing. Automatic fabric spreading machines can enhance the cutting room’s operations and require less manpower to manage them. In a nutshell, they can speed up the fabric layering process and improve the production rate.
Cutting machine

Each garment and fabric sheet needs to be cut into patterns. They are either cut manually or automated by computerized machinery. Types of cutting machines include straight knives, round knives, band knives, and hand shears. A few parameters that are required to be maintained during the cutting process are the machine’s cutting speed, duration, angle, and distance. For cutting smaller garments with accuracy, a band knife machine would be most useful. Whereas, for cutting more plies, round knives and computerized knives are more effective. Automatic cutting machines are helpful especially when cutting laces.
Sewing machine

Sewing machines are the engineering core of garment manufacturing. The different types of sewing machines include single needle, double needle, multi-needle, overlock, flatlock, long-arm sewing machines, and much more. Before selecting a sewing machine, it is essential to buy one that is specialized to deal with either heavy or thin fabric. The motor is also important to consider as servo motors generate less noise compared to clutch motors. The seam length and the contour shape are two parameters that can affect the sewing machine’s operation and stitching efficiency. To manage large quantities of fabric, long-arm sewing machines are most helpful when working with heavy fabrics and embroidery stitches.
Fusing machine

Fusing machines are used to fuse a material through the exchange of heat and pressure. As a result, the fused material will have enhanced fabric strength and withstand frequent wash. This is a crucial process in determining the quality of the garment. Maintaining an optimum level of temperature, pressure, and processing time are three key parameters to keep in mind when operating a fusing machine. Different types of fusing processes include flatbed, continuous, high-frequency, and hand iron. The continuous fusing press is the most used fusing machine in the garment industry, whereas, a high-frequency fusing machine has a high production rate as the material between the fusing plates moves at a very high speed.
Embroidery machine

To add embroidery patterns, having an embroidery machine can save time. With digitalized embroidery machines, the turnaround time will be a lot quicker than with traditional hand embroidery. One can give their design outline and get it transferred onto the garment by the embroidery machine. Maintaining these proficient machines can increase production rates and provide scalability to patch embroideries on different types of garments.